Mercuries Data Systems, with over 40 years of experience in maintenance management, consistently collaborates with clients to address their equipment management needs and fully comprehend the challenges they face. In response, ServiceJDC has developed a cutting-edge equipment management module to streamline maintenance operations. Before delving into the module's features, let's explore the hurdles encountered in traditional equipment maintenance management.
Lack of transparency in engineers' work schedules, making it difficult for supervisors to know the status of tasks and track progress. Assigning ad-hoc cases becomes a challenge.
Managing multiple types of equipment often involves the cumbersome task of manually entering data on paper forms, followed by the need for computer input. This process is time-consuming, labor-intensive, and inconvenient when it comes to retrieving information later on.
Lack of detailed records on troubleshooting methods, making it difficult to quickly retrieve information to solve similar problems in the future. Experience transfer becomes challenging.
The equipment management module efficiently tackles these challenges by providing a platform to configure and manage equipment models, names, customer information, installation locations, warranty periods, required technical expertise, and more. By seamlessly integrating it with the "Task Management" module for work assignments, the "Customer Management" module for tracking equipment history, and the "Form Management" module for data collection, analysis, and statistics, you gain comprehensive control over all aspects of maintenance management. This enables the seamless implementation of intelligent equipment maintenance management practices.
Advantage 1: Highly Flexible and Customizable Data with Extended Fields for Easy Equipment Database Setup
1. Customized Data: Related Fields for Efficient Selection
Before enabling equipment management, we recommend creating custom data. This allows you to edit and define the necessary information, such as product details, parts lists, and model tables. By doing so, personnel can quickly select and associate relevant information in any desired format, eliminating the time-consuming task of manually filling in each record.
In the "System Setting > Custom Data Maintenance" section, you can easily create new data names and design data structures by clicking on "Add". Using drag-and-drop functionality, you can establish the desired data format. For instance, in the vendor model table, you can design machine categories and models. By clicking on the green box of the data, you can add individual records or import vendor model data in batches. This streamlined process enables you to efficiently build the foundation of equipment management when designing "Equipment Data" in the extended fields, automatically filling in associated field data.
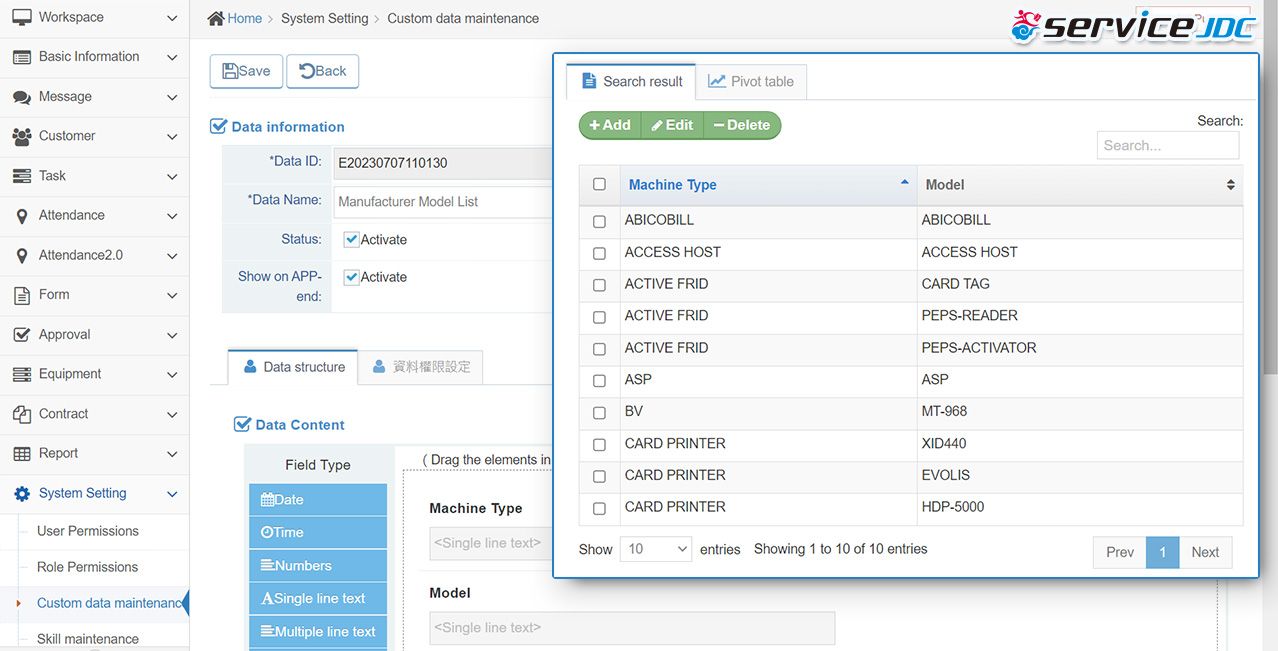
Figure 1: ServiceJDC Custom Data Maintenance and Adding New Data
2. Field Extension: Flexible Customization to Meet Your Specific Needs
In the” Expansion Field” feature, you have the flexibility to customize the required fields for "Equipment Data" and "Equipment Error Code" based on your specific needs. This includes fields such as equipment model, name, image, customer name, warranty period, installation location, maintenance techniques, and more.
The single-selection field functionality makes data entry quick and convenient. In the advanced settings of the single-selection feature, you can choose associated fields from the provided option list. You can define the source data, option hierarchy, and display fields in the association rules. With these rich and flexible configurations, you can create customized equipment forms that perfectly align with your requirements, allowing you to build a comprehensive and exclusive equipment database for your company.
Advantage 2: Precise Assignment, Real-time Tracking, Mobile Query - Integration of Information Connecting Company Internally and Externally
By integrating equipment management with the equipment task feature, ServiceJDC allows for the precise assignment of personnel to specific equipment. This enables quick access to relevant equipment information, including maintenance records and troubleshooting details. Additionally, it supports the maintenance of employees' skills by ensuring a rapid and accurate understanding of equipment history, and facilitating the assignment of the most suitable repair personnel. This integrated approach helps companies optimize their repair processes and effectively address any deficiencies in assignment procedures.
1. Optimized Assignment
After activating the equipment management module, you can utilize the task module to add equipment tasks. The system provides customizable equipment query conditions, including the Professional Skills Field, which allows supervisors to quickly identify personnel with the required repair skills (Note: Set up in System Setting > Skill Maintenance). Furthermore, employee and shift schedules assist in identifying available and working employees for temporary tasks, ensuring efficient and accurate assignment of temporary repair tasks.
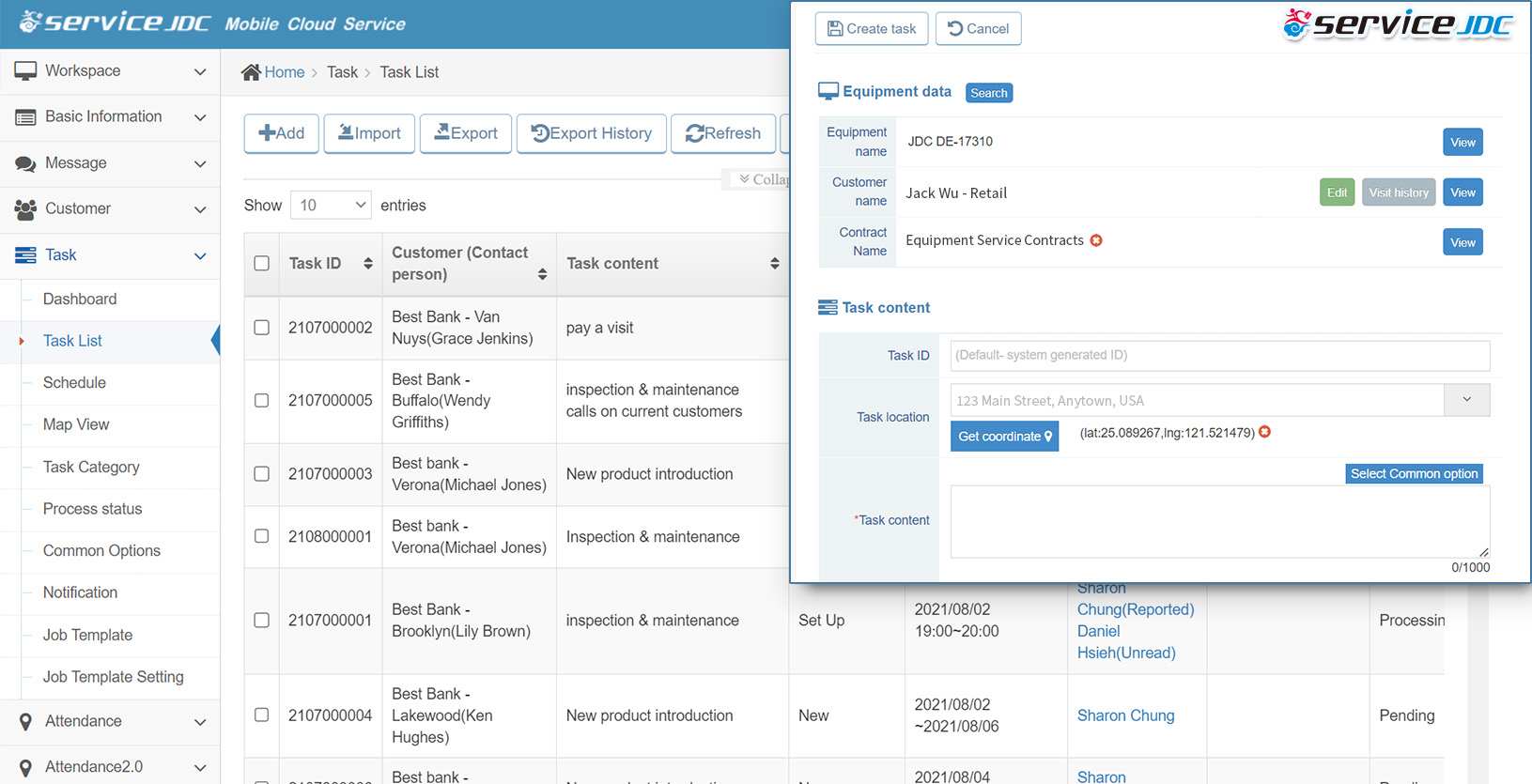
Figure 2: Equipment Task Assignment
2. Real-time Tracking
Customers with the equipment management feature can utilize the task dashboard to query and analyze equipment tasks. With customizable query conditions such as time and equipment names, efficient tracking and analysis of specific equipment tasks during specific periods become possible. Moreover, diverse analysis methods, including the "Equipment Map," offer detailed equipment information based on geographic locations.
3. Equipment Knowledge Base
In addition to recording detailed equipment information in the equipment data, we have implemented the "Equipment Error Code" feature to identify the causes of equipment malfunctions. This feature allows enterprises to customize a failure code table specific to each piece of equipment, including equipment types, failure descriptions, troubleshooting methods, and more. By doing so, a comprehensive knowledge base for equipment and fault handling is established, facilitating efficient and effective maintenance operations.
During fieldwork, maintenance personnel can easily access all essential equipment information, including basic details, historical tasks, failure codes, and troubleshooting methods, all through their mobile phones. This enables them to familiarize themselves with the equipment's record before starting the job and carry out their tasks quickly and accurately, ultimately enhancing customer satisfaction.
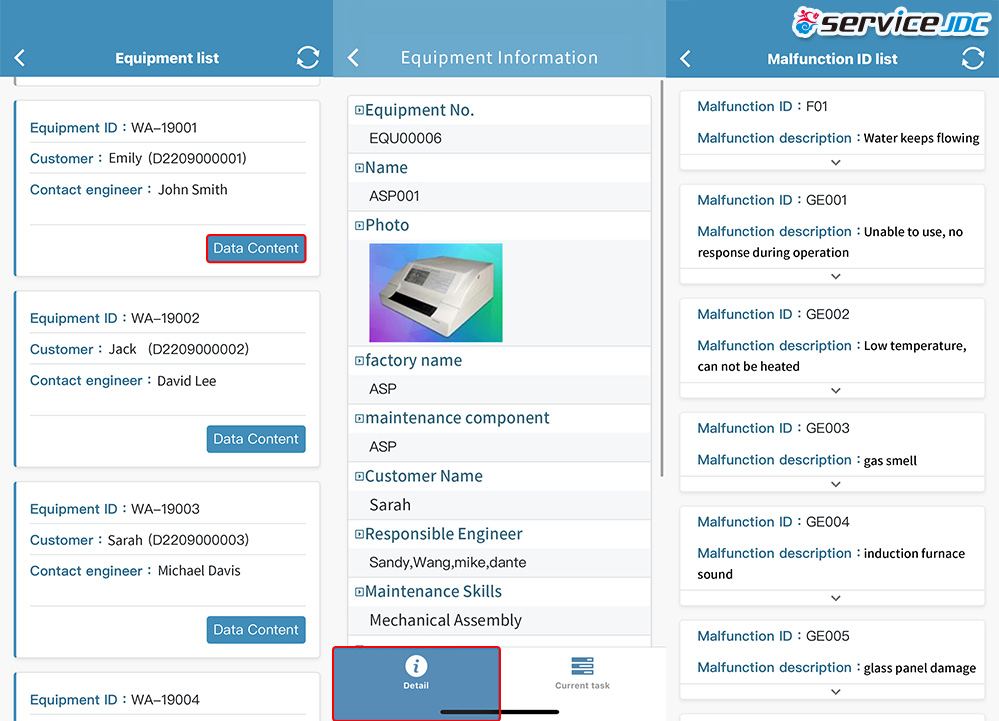
Figure 3: ServiceJDC Mobile App - Equipment Information and Failure Code List.
Advantage 3: Digitized Forms for Instant Analysis - Enhancing Team Competitiveness
Even equipment tasks can incorporate customized forms, seamlessly integrating equipment management, task modules, customized forms, and data analytics.
Let's illustrate the process of creating forms using related fields and utilizing pivot analysis to analyze machine failure causes, repair time requirements, and personnel performance.
1. Form Design: Application of Related Fields
ServiceJDC's innovative Customized Data feature allows flexible utilization of "related fields" in various forms. To display equipment failure codes and their descriptions through association and cascading drop-downs, follow these steps:
- Create a selection function in the maintenance form.
- In the selection settings for "Failure Code," choose the related field and select equipment failure codes as the data source.
- In the selection settings for "Cause of Failure," select the same option as the equipment failure codes and set the cascading relationship as "Failure Code = Failure Code."
- Choose to display the description field for the failure code.
With this setup, personnel can quickly and easily complete the selection process during their work.
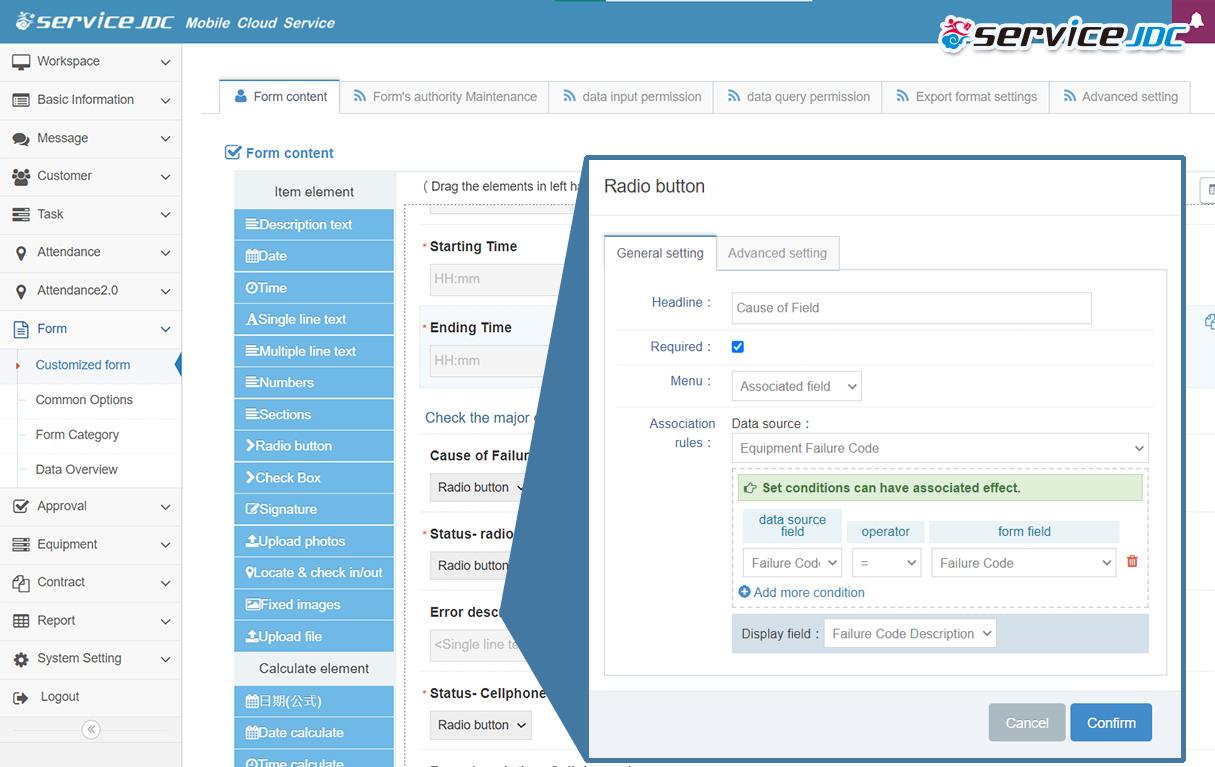
Figure 4: Customized Forms and Related Fields.
2. Pivot Analysis: Analyzing the Causes of Equipment Failures
After field personnel collect data, they can utilize ServiceJDC's "Data Overview" feature to generate pivot reports and analyze equipment failure causes. By selecting the desired time range and extracting relevant categories and codes, businesses can gain valuable insights into failure causes and personnel performance. ServiceJDC's comprehensive equipment management, related fields, and form analysis functionalities empower data-driven decision-making, leading to optimized maintenance operations.
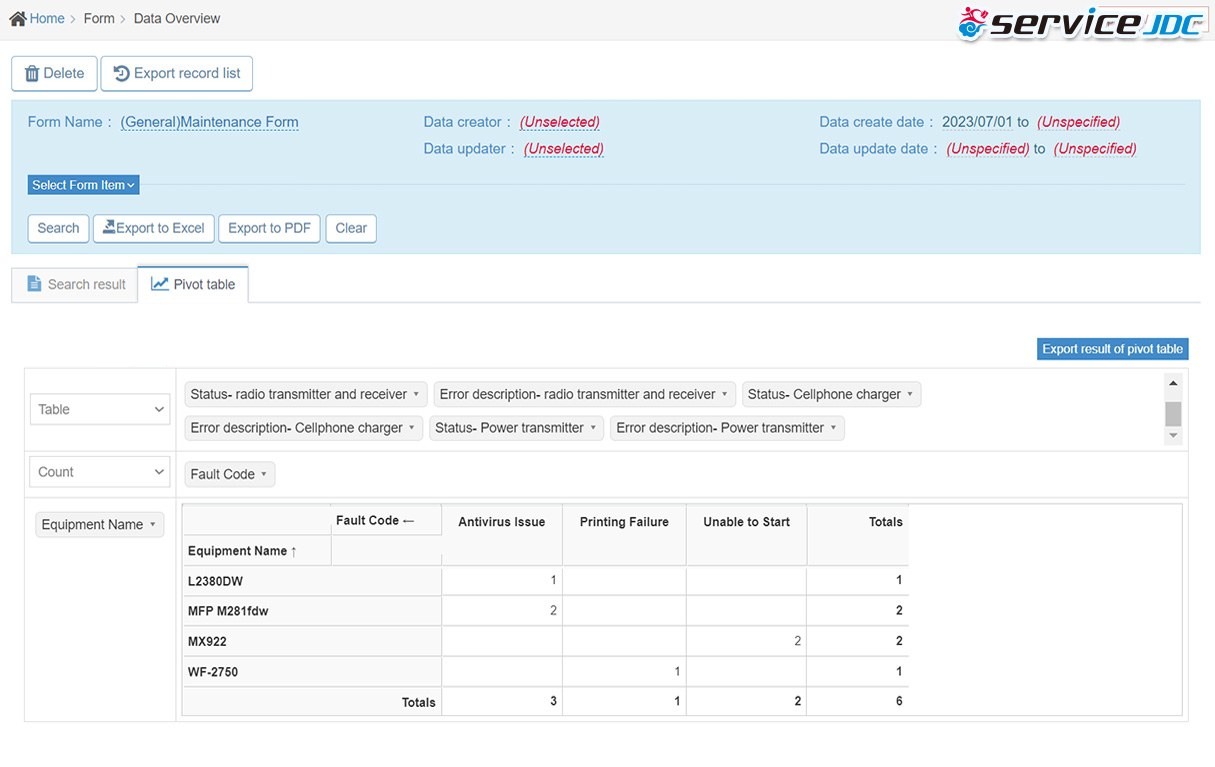
Figure 5: ServiceJDC's Form Data Analysis for Equipment Tasks
Streamlined Maintenance Operations - Boosting Competitiveness through Digital Management
ServiceJDC's equipment management system seamlessly integrates with task modules, form tools, and statistical analysis functionalities. Field personnel can collect and report form data on the go, while managers have quick access to data for analysis. This enables intelligent equipment maintenance management and enhances service quality and competitiveness.
Mercuries Data Systems, an experienced system integration provider, understands the unique challenges businesses face in maintenance, distribution, construction supervision, and co-marketing. The cloud-based field management system, ServiceJDC, is designed to address these pain points and empower businesses with data-oriented approaches. Through data analysis and innovative technologies, businesses can optimize operations and achieve success in today's digital landscape. Visit the ServiceJDC official website for more information.